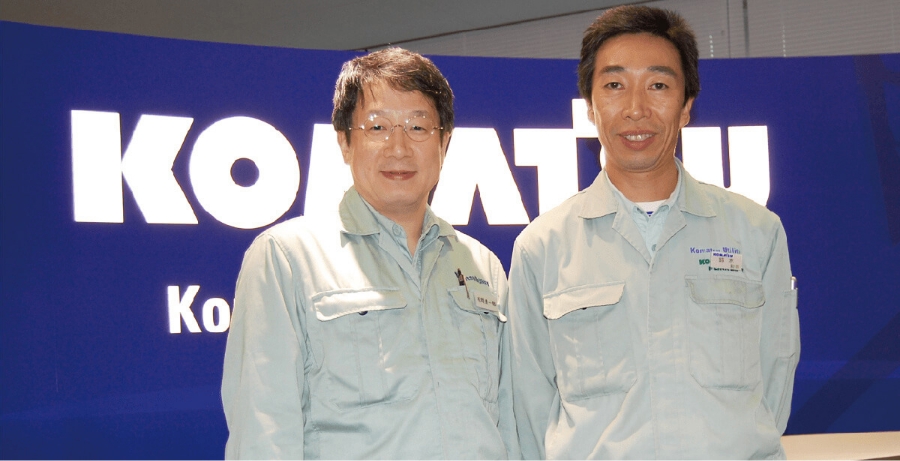
導入事例:RaLC
コマツ(株式会社小松製作所) 様
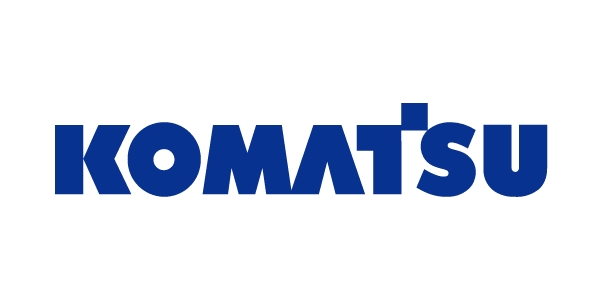
物流改善に「RaLC」の位置情報管理を活用。
フォークリフトの位置、動線の把握によりコスト削減を目指す。
導入前の課題
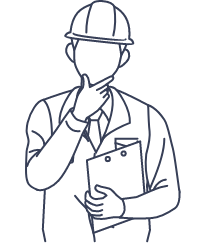
- 「コマツウェイ」に明示された「現場主義」を効率的に実践したかった
- 工場内における作業の「見える化」を図り、物流 改善のポイントを現場と共有したかった
- 物流車両を削減し、少ない台数で効率的に運用したかった
→
導入ポイント・導入効果
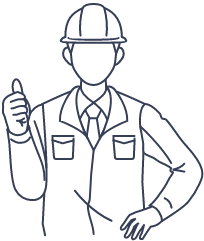
- すでに導入していたRaLCを活用して、短期間でコスト削減の可能性を検証し、具体的な実践に移すことができた
- フォークリフトの1日分の動線解析を、RaLCで30分に短縮できるようになった
- 物流車両のさらなる削減に向けた計画など、物流改善の取り組み強化につながった
モノ作りの現場から率先して改善に取り組む「現場力」
“現場主義”を実践するためICTを活用したシステムの導入を検討
社名の由来「ユーティリティ」について、総務部の松岡 圭一郎氏はこう語る。「“ユーティリティ”というのは耳慣れない言葉ですが、海外では多目的に使われる小型の産業機械をそのように呼びます。当社は、コマツグループにおける“ユーティリティ”、つまりフォークリフトと小型建機の生産・開発を担っています」。
フォークリフト事業と小型建機事業の統合、さらに本社・工場の集約によって、効率的な製品開発が可能になった。その一例が、油圧式無段変速機構(HST)と呼ばれる駆動方式を採用した新型フォークリフトの開発だ。
エンジンと油圧システムを併用し、CO2の排出量の削減を実現するフォークリフトで、今後製品化される予定となっている。
「新型フォークリフトの変速機構には、ミニ建機で培った技術が活かされています。このように、フォークリフトと小型建機という異なる分野の技術力を相互に生かせる環境が、当社の大きな強みとなっています」と松岡氏は説明する。
コマツグループでは、創業以来、先人が築き上げた企業としての強みや価値基準、それを実行する行動様式などを取りまとめ、「コマツウェイ」として明文化し、受け継いでいる。
「現場主義は、“実際に自分の足で現場に赴き、自分の目で問題点を観察し、解決する”という考え方です。しかし、すべての現場を見回っていては、手間と時間がかかってしまいます。そこで、ICTによって現場を“見える化”し、離れた場所から問題点を発見できる仕組みを構築しようと思いました」と栃木工場 工場管理部 生産管理課 主任の鈴木 和幸氏は語る。
2009年初頭に、ワーキンググループを社内に発足。システム導入に向けたプロジェクトを開始した。しかし、当時は「試行錯誤の連続だった」(鈴木氏)という。
まず最初に取り入れたのは、GPSだった。物流車両(フォークリフトなどの構内運搬車両)1台1台にGPS端末を取り付け、動線を明らかにしようとしたが、屋内に物流車両が入ると、構内での位置関係が正確に把握できない問題があった。
RaLC 導入の狙い/効果
サポート力に対する信頼に加えて、動線解析の時間を大幅削減した実力を評価
次に、GPSの代わりに、車載カメラを物流車両に搭載した。車載カメラからの映像をもとに動線を紙に書き写して、物流車両の動きを明らかにしようとした。しかし、1日あたり約8時間の動画を解析する負担は、相当大きかったという。
「工場内で稼働する物流車両を解析するために、12人がかりで2週間もかかりました。また、車載カメラの電池が、半日で消耗してしまうため、何度も電池を入れ替えるなど、細かい点での苦労もありました」と鈴木氏は振り返る。
試行錯誤を繰り返す中で、GPSや車載カメラではなく、車両の“XY座標”を時系列で把握でき、それを構内のマップ上に展開することができれば物流車両の位置や動線を再現することができると考えたのだ。そこで鈴木氏は、シーイーシーなど各社が提案するシステムの検討を開始した。
「当社は以前より、物流システム部門や生産技術部門に、他の“RaLC”シリーズを導入してきました。すでに工場の3Dモデルがシミュレーション上に構築されているため、コストを抑えながら新しいシステムが稼動できると判断しました」(鈴木氏)。
また、シーイーシーのサポート力も選定の大きな決め手になったという。「以前、“RaLC”に新しい機能を追加するように、シーイーシーにお願いしたことがありました。後日、バージョンアップでその機能がすぐに追加された時は驚きましたね。海外製品のサポートでは、このようなスピード感はあり得ないと思います」(鈴木氏)。
その後、ハードウェアの選定などを経て、2010年4月よりシステムが本格稼動した。
現在の運用方法は、
(1)物流車両に搭載した「アクティブRFIDタグ」が定期的に電波(無線LAN)を発信
(2)アクセスポイントが「アクティブRFIDタグ」からの電波を受信
(3)電波強度をもとにポジショニングエンジンが三角測量を実施
(4)XY座標をもとに「RaLC 位置管理システム」が物流車両の位置情報をマップに展開
という流れになっている。
工夫点としては、「アクティブRFIDタグ」から発信される電波をアクセスポイントが受信し、ポジショニングエンジンで平均値を出してからRaLCへ位置情報を送っていることが挙げられる。「平均値を出さないと、電波のバラツキにより動線が正確に表示されません。
そのため、複数回の位置情報の平均をとり、バラツキを抑えるようシステムを改善しました」と鈴木氏は説明する。
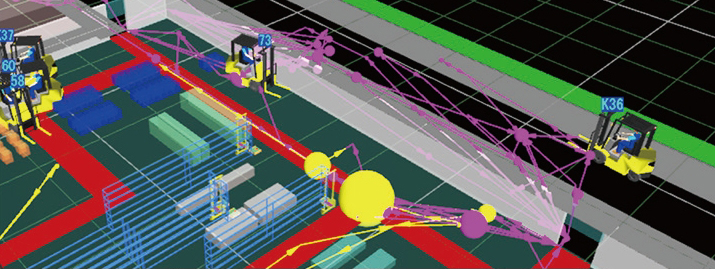
フォークリフトの車両位置や導線、滞留箇所などをリアルタイムに「見える化」
今後の展望について
生産車両の進捗管理を見える化し、さらなる品質と信頼性の向上を図る
同社は現在、「RaLC」の位置管理システムによる解析を通じて、無駄な動線が多い物流車両を発見し、削減する取り組みを行っている。1日分の動線を解析する時間は、30分もかからないという。「以前に比べて、解析にかかる時間が大幅に削減できました。そのため今では、数日分のデータをまとめて解析しているほどです」と鈴木氏は笑顔を見せる。
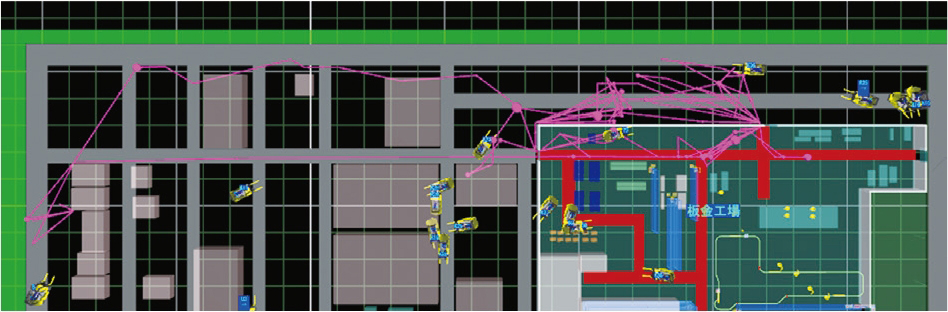
生産ライン全体を位置情報と物流業務最適化支援ツール「RaLC」で再現している
今後の目標は「さらなる物流改善を目指すため、RaLCを使って現場の生産性向上を図る」(鈴木氏)ことをかかげている。同社は2009年から物流車両の削減に取り組んできた。これまでに30台ほど削減したが、RaLCの位置管理システムを活用して、稼働時間と走行距離を分析しながら、さらなる高効率運行を進めていく構えだ。
このほかの取り組みとして、
(1)「RaLC位置管理システム」を活用した構内オペレーターへの指示システム
(2)部品へのRFIDタグの展開
(3)Web画面を使った生産車両の「見える化」
といった施策も検討している。また、物流関係のお客様が多い同社ならではのトピックもある。「RaLC位置管理システム」を活用した取り組みに、多くのお客様が関心を寄せているというのだ。
「このシステムは、フォークリフトが実際の現場でどのように動き、使われているかを観測する初めての試み。かつてないデータの蓄積が、新しい改善方策や、新しい仕事のやり方を生みだす可能性を秘めています。そうした『可能性』を、物流に携わるお客様は敏感に感じ取っておられるのではないでしょうか」と松岡氏は意気込みを語る。
世界でも類を見ない位置管理システムを活用するコマツユーティリティ。同社の「見える化」に対する取り組みは、製造・物流業界はもちろんのこと、日本の産業全体に大きな刺激を与えることだろう。
※製品名・企業名・役職名など、記載の情報は取材時のもので、閲覧時には変更されている可能性があります。

- 設立
- 1921年(大正10年)5月13日
- 代表者
- 代表取締役社長(兼)CEO 野路 國夫
- 資本金
- 連結678億70百万円(米国会計基準による)
- 本社所在地
- 〒107-8414 東京都港区赤坂2-3-6
- 従業員数
- 連結:41,059名 単体:8,210名
- 事業内容
- 建設・鉱山機械、ユーティリティ(小型機械)、林業機械、産業機械などの事業
- URL
- https://home.komatsu/jp/