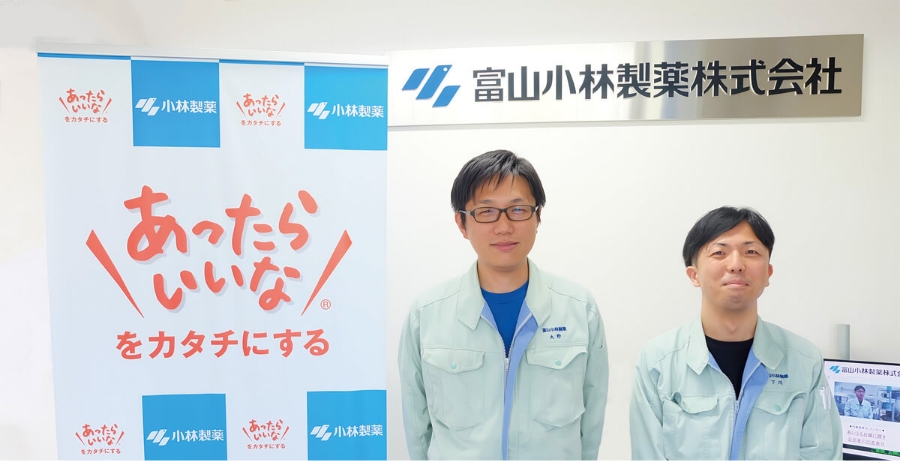
導入事例:WiseImaging
富山小林製薬株式会社 様
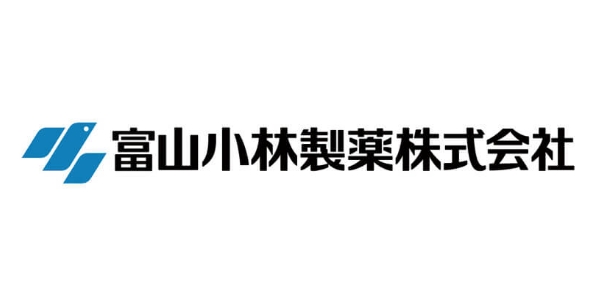
導入前の課題
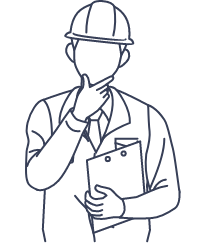
- 増産に対応するために目視検査員の人員確保に苦慮
- 従来の画像検査では20%の見逃し、30%の過検出が発生
- 自社で工程をメンテナンスできる知見の蓄積と体制の確保
→
導入ポイント・導入効果
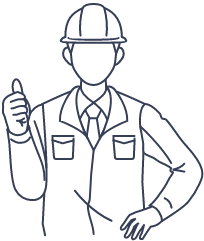
- 目視検査員の省人化と3割の増産対応を両立
- 見逃し率0%、過検出率2%と高精度の検査をインラインで実現
- AI技術の手の内化に成功、別ラインへの横展開も決定
導入の背景・課題
グループ最大規模の工場で、日々ラインの正常稼働を支える
国内外合わせて13の生産工場を抱える小林製薬グループの中で、最大規模を誇る工場が富山小林製薬株式会社。医薬品・医薬部外品から衛生雑貨品・日用雑貨品に至るまで400アイテムを超える製品を製造するなど、同社は小林製薬グループの屋台骨を支えている。
同社には大きく2つのカテゴリーがあり、ひとつは芳香剤や入れ歯洗浄剤などの日用品グループ。もうひとつは健康食品や医薬品、化粧品などを生産している薬粧品グループだ。さらに、この2つのグループは中身の製品そのものを製造する調剤グループと調剤された中身を充填する生産グループで構成されている。生産部 薬粧品生産グループ ライン長 大野 裕辰氏は「我々の主な業務は、薬粧品の中身を充填するラインや設備の保守・メンテナンスです。生産に支障が出ないように日々ラインの正常稼働に務めています。」と語る。
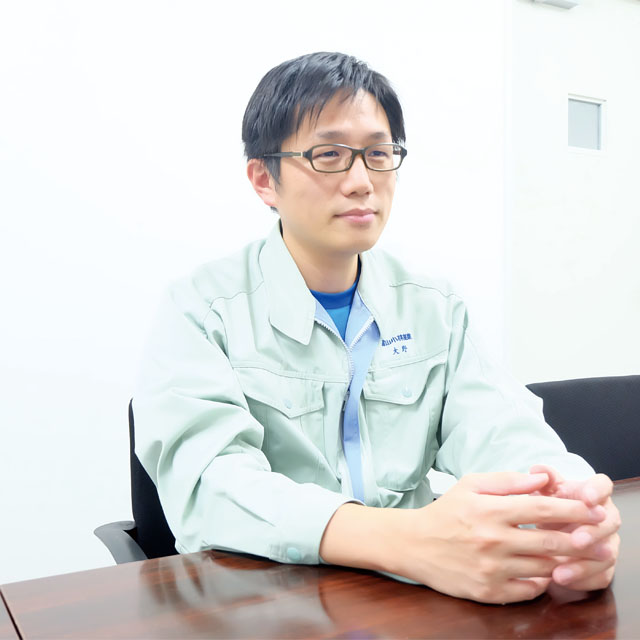
生産部 薬粧品生産グループ ライン長
大野 裕辰氏
包装の検査工程に課題
薬粧品を生産するラインにはさまざまな工程があり、検査工程もそのひとつ。その検査工程で活躍しているのはキーエンス社の画像処理システムXG-Xで、ほとんどの製品は生産時の不具合をこれで判定できる。
ところがこの十年来、XG-Xをもってしても正確な判定が難しい製品があった。「上下と横の3箇所にシールを行うのですが、ここにタックができてしまった場合はNGとなります。しかし、EDICARE EXの包装には光沢があるため、光の加減によって判定が難しく、良品をNGと判定してしまう過検出が多発していました(図1)。」(大野氏)
また、生産部 薬粧品生産グループ 下川 一輝氏は「キーエンスのエンジニアにも協力いただいてシステムを調整しましたが、過検出率は約30%、見逃し率は約20%までが限界。そのため、EDICARE EXのラインには専任の検査員を配置し、目視での検品業務を行っていました。もちろん、XG-Xの性能には問題がなく、ほかの製品では素晴らしい判定をしてくれているだけに、もどかしい思いがありました。」と語る。
EDICARE EXは市場で人気を博していたため、増産になったことも生産体制に影響を与えた。「通常の生産体制から2交代勤務の体制になりました。そうなると昼と夜で2人(2ラインのため計4人)の検査員を確保しなければなりません。特に夜間勤務が可能な人材は少ないため、ラインの人員のやり繰りに苦労しました。」(大野氏)
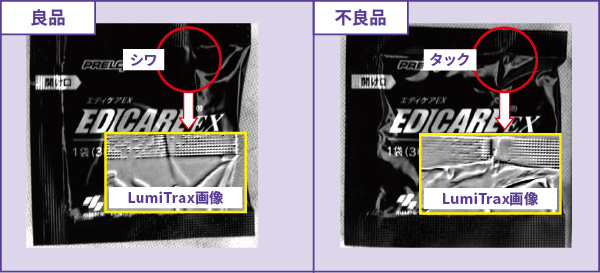
図1:EDICARE EXの良品と不良品の違い
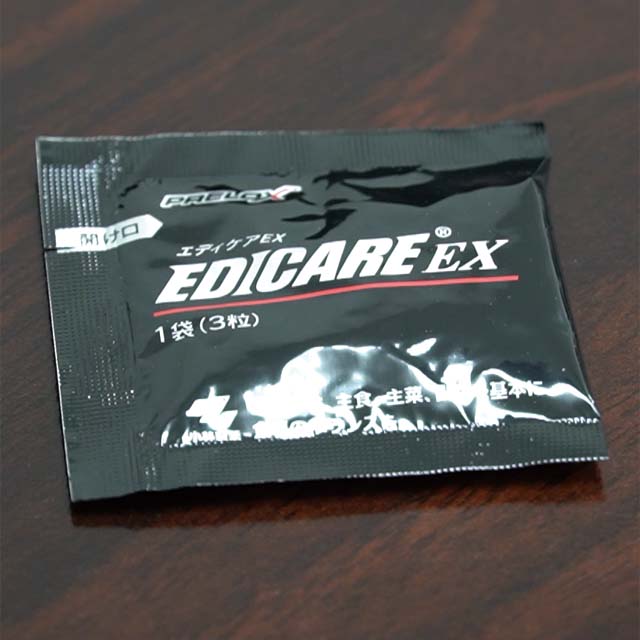
光沢があるEDICARE EXの包装
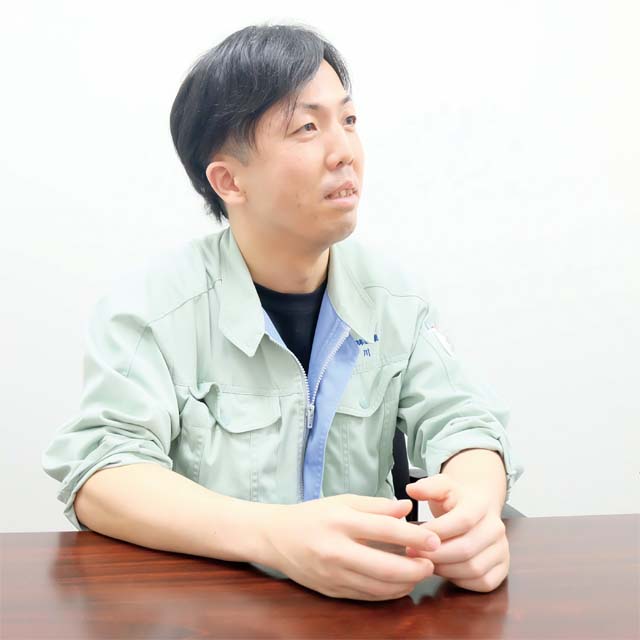
生産部 薬粧品生産グループ
下川 一輝氏
導入の選択と決断
部内でAIの取り組みを検討
そんなとき、部内のあちこちからDXへの取り組みの声が聞こえるようになった。そこで、部内でのDXへの取り組みを明確にするため、テーマに掲げたのがAIだった。AIを活用することで生産性の向上や業務改善が期待できる工程を精査していくなか、スポットが当たったのが前述したEDICARE EXの検査工程。判定問題、人材確保に課題を抱えていただけに、AIで解決できるならと考えて導入の道を探ることになった。
トライアルの精度を見て導入を決定
最適なAIを選定するフェーズでは、ネット検索のほかセミナーなどにも出向き、6社ほどのAI製品をピックアップ。実際に話も聞いたが、総じて高価なことがネックだった。「AIに取り組むといっても、潤沢に予算があるわけではありません。どんなメリットが得られるか分かりませんから、安価にスモールスタートできる製品を探していました。」(下川氏)
シーイーシーのWiseImagingに出会ったのは、富山県にあるシステム会社からの紹介だった。あらかじめ価格が明記されており、しかも安価。これなら導入できるかもしれないと思い、早速シーイーシーにアポイントを取った。
シーイーシーの話を聞いた後、次に行ったのは導入できるかどうかを判別するための有償トライアル。オフラインで撮影したさまざまな角度からの画像(良品、不良品それぞれ一定数)と位置補正データを記載したサンプルを渡し、シーイーシー側で検査モデルの構築を行った。その結果、98%という高い精度をマーク。これを踏まえ、WiseImagingの導入が決定した。導入後の進捗は表の通りだ。
2019年7月 |
ライセンス購入 |
2019年7月~ |
AIの学習期間&オフラインでのテスト |
2020年6月~ |
インラインでのテスト&オフラインでの調整 |
2021年3月 |
本稼働 |
また、図2の通り、本稼働後もXG-Xを活用している。「すべてWiseImagingで処理させる必要はないと思っており、シールの幅や真っすぐカットされているかなどの判定は、XG-Xで処理するほうが合理的だと考えていました。工程的にはXG-Xの後にWiseImagingが処理するのですが、この連携と制御を行うため、キーエンスのPLC製品KV-8000も新たに導入しました。」(大野氏)
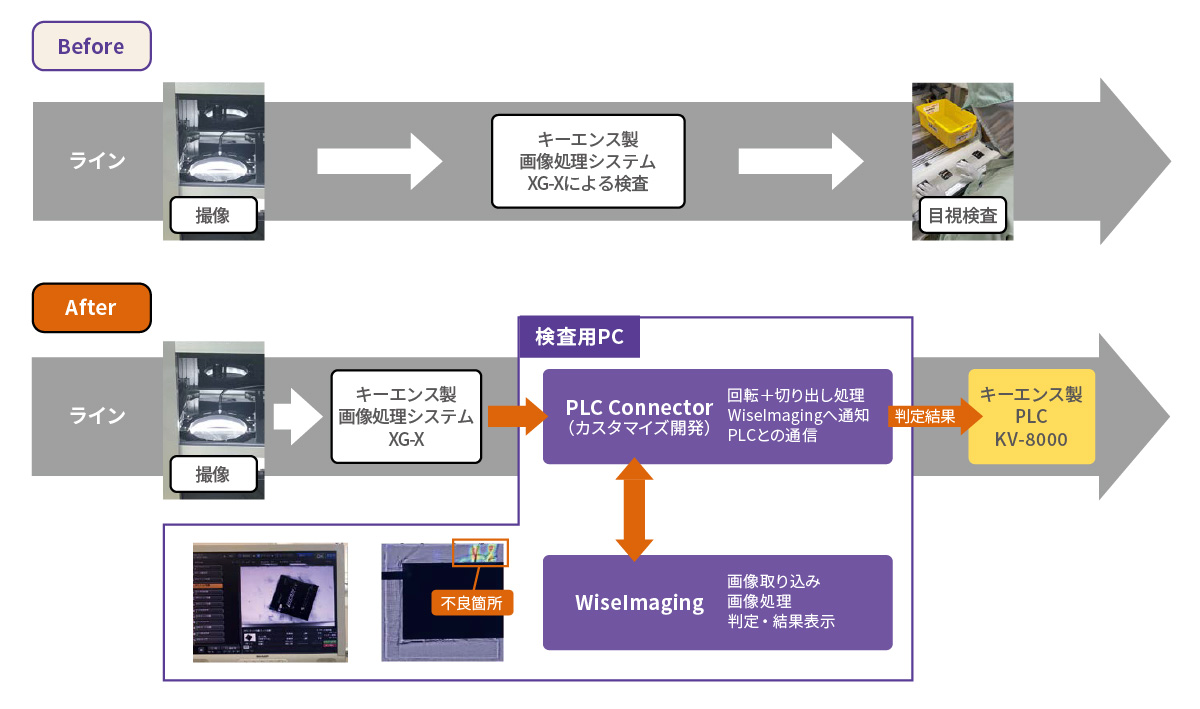
図2:WiseImaging導入前後での検査工程の違い
取り組みと効果
知見の蓄積へ自ら検査モデルを構築
今回、同社におけるWiseImagingによるAIの取り組みの大きな特徴は、検査モデル構築を自社で実施したこと。「何もかもシーイーシーに任せていては、不具合やトラブルが起こった際に自社で対応できません。何かあった場合に対応するのは、速やかに動ける現場の我々でなければなりませんから、自分たちでAIの学習を進めるべきだと考えました。」(下川氏)
「AIの知見を蓄積したいという狙いもありました。キーエンス製品を導入したときも同じ考えで、我々自身で調整した部分がかなりあります。知見が貯まれば横展開も容易なので、AI導入を成功させれば工場のさまざまなところで活用できるのではないかと考えました。」(大野氏)
もちろん、検査モデルの構築は簡単ではなかった。不良サンプルの画像を集めるところからスタート、日々WiseImagingに学習させた。「当初はなかなか学習がうまく進みませんでした。ラベルの作り方を変更するなどして徐々に学習がうまく進むようになりました。そういう意味では、シーイーシーのサポートにかなり助けてもらいました。学習させるポイントや注意点など、さまざまなアドバイスをもらいながら進めていった感じです。」
インラインに導入できる精度を目指す
ライセンス購入から本稼働までに要した時間は約1年半。これについて大野氏は「AI導入前にいろいろと調べていましたから、それぐらいの時間がかかることは想定済みでした。大事なのはインライン化しても問題ない精度の確保。見逃し率は0%を達成しないとラインに入れられません。過検出率もできる限り低減したい。時間がかかってもインライン化できる精度を目指すため、下川をWiseImagingの専任にしました。」と語る。
専任といっても、一日の大半をWiseImagingの業務に費やしているわけではない。「業務の割合を再分配してもらいましたので、身体的な負担はありませんでした。そもそも画像を取捨選択してWiseImagingに読み込ませてしまえば、次にPCに向き合うまで時間の余裕ができます。これで、一日の半分は本来のメンテナンス業務やAIの知識を習得する時間に当てることができました。」(下川氏)
検査員ゼロ、3割の増産に対応
2020年6月以降は、インラインでのテストとオフラインでの調整の繰り返し。オフラインのテスト環境では98~99%の精度が出ていても、インラインの本番環境では60%程度に落ちてしまったため、さらなる画像の読み込みなどの調整を行って精度を高めていった。2021年3月には、ついに本稼働がスタート。ようやく十年来の課題が解決した。
「現在、問題なく稼働しています。効果としては、目視の検査員が不要になり、人的リソースの最適化が可能になりました。実際、タイミングよく増産がかかり、2交代制勤務から3交代制勤務へシフト。この場合、従来なら3人の検査員が必要でしたが、今は不要になったため、ラインの中で再配置できるようになりました。ライン自体のスピードも従来と変わっていませんから、3交代制勤務だとライン1本分、約3割り増しの増産に対応可能。経営層からも高い評価が得られています。」(大野氏)
「初日、本稼働しているシーンを見たときは感慨深いものがありました。目視の検査員がいないという目に見える結果が出ているわけですから、やり遂げて良かったと心から思いました。」(下川氏)
今後の展開と期待
2本目のラインにも導入予定
EDICARE EXのラインは2本あり、今回WiseImaging導入したのは1本のみ。今回の成功を機にライセンスを追加購入し、2本目のラインにもWiseImagingを導入していく予定だ。「物理的なところに若干の誤差があるため、多少の微調整は必要になると思います。しかし、基本は同じラインですから、2本目の導入は時間がかからないと思っています。」(下川氏)
「社内には本当にできるのか?という声もありましたが、DXやAIと言われている時代でチャレンジしない手はないと思い、ここまで続けてきました。結果が出たときは本当に嬉しかったですね。これも、安価にWiseImagingを提供してくれたシーイーシーのおかげです。ライセンス購入後のサポートにも満足しています。引き続きよろしくお願いします。」(大野氏)
使用者の
感想
ラインや設備の保守・メンテナンスに従事する傍ら、AI画像検査の専任としてモデル構築を担当された生産部 薬粧品生産グループ 下川 一輝氏に、今回の取り組みに関する感想を伺いました。
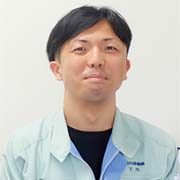
今回の取り組みは、AIの知識がまったくのゼロからのスタートでした。本当に知らないことだらけで、マニュアルを見ても単語で躓いていました。そこでまずは、ネットの検索やシーイーシーのサポート に確認するなどして片っ端から調べました。分からない単語を調べながらだと、調べている最中にさらに分からない単語が出てきます。それで、また調べるという繰り返しですね。
でも、根気強くやっていると、調べる頻度はどんどん少なくなっていきます。調べていると興味も湧いてくるので、さらに深掘りして知識を蓄えていきました。AIはもちろん、これからもさまざまなことにチャレンジしていきたいですね。(下川氏)
※製品名・企業名・役職名など、記載の情報は取材時のもので、閲覧時には変更されている可能性があります。

小林製薬グループの一員として1982年3月に設立。医薬品・医薬部外品から衛生雑貨品・日用雑貨品など、400アイテムを超えるさまざまな製品を製造している。さらに、小林製薬で研究・開発された製品を“商品化” するための試作や検証(バリデーション)、承認申請や生産設備の企画、製造段階での検証も実施。試作・生産準備・品質管理を行う「コンカレント開発方式」の採用により、ひとつの製品が企画されてから店頭に並ぶまで平均13カ月(医薬品を除く)というスピード生産を実現。富山に根づく企業として、地域の方々に誇りを感じてもらえる企業になることを目指している。