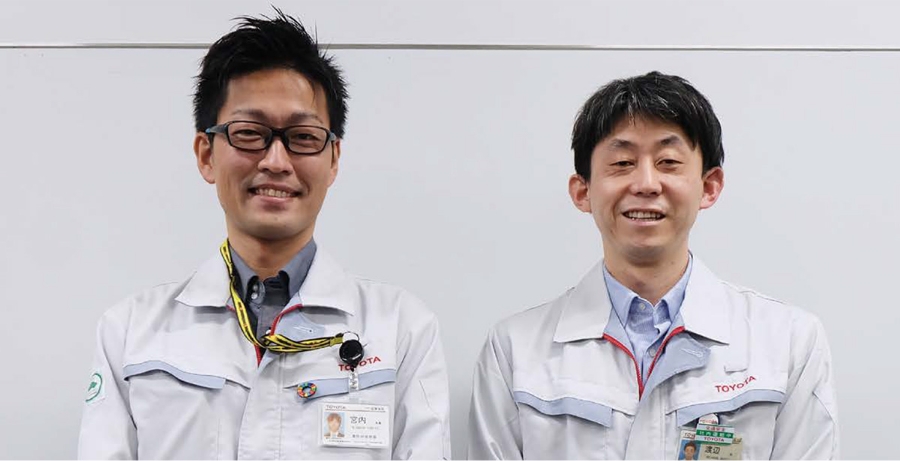
導入事例:WiseImaging
トヨタ自動車株式会社 様
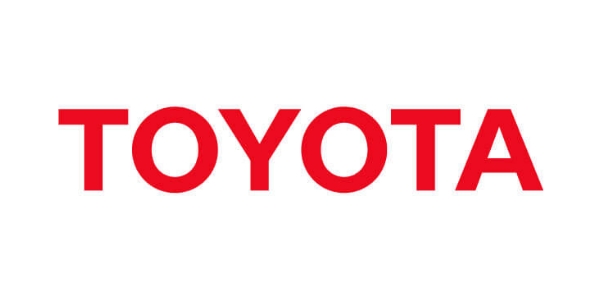
導入前の課題
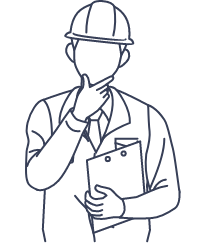
- 省人化につなげる自動化の取り組みで、人に頼らざるを得ない検査工程がネックに
- 検査対象は複雑な形状であり、検査の難易度も高い
- 検査の自動化による省人化が部門ミッションの1つだが、なかなか進まない
→
導入ポイント・導入効果
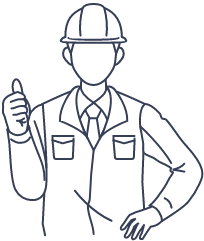
- 検査の自動化で生産ラインのフルオートメーションを実現
- 画角ごとに検査モデルを構築することにより、絶対条件である見逃し率ゼロを達成
- 同工場内で初めて検査の省人化を実現、モデルケースとなり部門全体の動きも活発化
導入の背景・課題
素形材の生産技術を支援
今回、トヨタ自動車でWiseImaging導入のお話を伺ったのは、素形材技術部 焼結技術室 主幹 渡辺 誠氏と素形材技術部基盤開発室 主任 宮内 良貴氏。素形材技術部は試作と量産の生産技術を融合し、クルマ開発のスピードアップを図るために新設されたモノづくり開発センターに属する部門で、金属を主体とする素材に鋳造や鍛造、焼結、プレスといった力や熱の処理を加えて成形する素形材の生産技術を支援している。「我々の部門は鋳造、鍛造、焼結、プレスといった素形材に関する部隊がすべて集結しており、素形材づくりに携わっている国内外の工場が号口(本生産で製品を流すこと)生産できるように、型・設備の設計や試作対応、ラインの生産準備を行っています。」(渡辺氏)
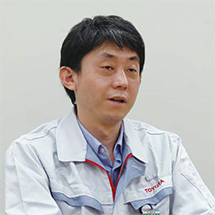
素形材技術部 焼結技術室 主幹
渡辺 誠氏
検査工程が自動化のネックに
クオリティの高い自動車をユーザーに提供していくため、トヨタ自動車ではさまざまなラインの自動化を図っている。しかし、著名なトヨタ生産方式を生み出したトヨタ自動車をもってしても自動化が難しい部分があった。それが人の目視に頼る検査工程だった。「自動化を図って原価を下げていく流れが、クオリティの高い自動車を提供する近道です。そうすると人件費が発生する目視検査は大きなネックです。単純な作業については、できる限り自動化もしくは検査レスで、省人化を実現していくのが我々の使命ですから、常にもどかしい想いがありました。」(渡辺氏)
そうしたなか、WiseImagingを先行導入していた本社工場の鍛造部が、フロントハブ部品の検査自動化に取り組み、インライン化を成功させ省人化につながったとの話が舞い込んだ。「自動化の成功事例ができたことは、他のラインでも実現できるのではないかという期待を高め、自動化に取り組むモチベーションを促すという意味で大きな意義がありました。もちろん、我々も同様です。早速、自動検査装置を導入するプロジェクトに取り掛かりました。」(渡辺氏)
導入の選択と決断
インライン化の実績を重視
自動検査装置のキーとなるのは、良品と不良品を判別するAI画像検査システム。素形材技術部では社内外における検査工程での自動化の取り組みに鑑みながら、最終的にはトライアルの実績を考慮し、WiseImagingを含む3つのAI画像検査システムをピックアップして比較・検討に入った。100枚程度の画像を学習させた場合の精度検証を経て、3カ月後に選定したのはシーイーシーのWiseImagingだった。その選定理由は以下の通りだ。
選定理由01インライン化に成功した唯一の製品
本社工場鍛造部がフロントハブの検査工程の自動化を成功させたAI画像検査システムこそがWiseImagingだった。「WiseImaging以外の2製品は、まだトライアルレベル。これに対し、インライン化という実績があるWiseImagingのアドバンテージは非常に大きなインパクトがありました。インライン化できているわけですから、精度は100%(不良品の見逃し率が0%)を実現しています。これから取り組む我々としては、ハードルが下がったような気がしました。」(宮内氏)
選定理由02国産メーカーの安心感
WiseImagingはシーイーシーが自社開発したAI画像検査システムだが、他の2製品は海外製品。常にメーカーと直でリアルタイムにやり取りできるのはシーイーシーだけだった。「検査工程の自動化は、AI画像検査システムのみで成り立つものではなく、カメラやデータ処理の機器などを組み合わせて検査装置をつくり上げていかなければなりません。その検査装置をつくる過程のなかで、精度や制御方法を詰めながら設備化していくわけですから、我々が望んだのはスムーズにやり取りできる密な協力体制です。そうなると、直でリアルタイムにやり取りできる国内メーカーのシーイーシーを選びました。」(宮内氏)
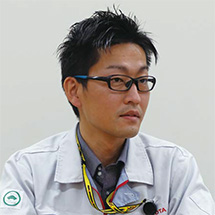
素形材技術部 基盤開発室 主任
宮内 良貴氏
自動化に向けた取り組み
複雑な構造のATキャリア
今回、自動化のターゲットになったのは、AT(オートマチック・トランスミッション)のキャリアと呼ばれる焼結部品の検査工程。検査工程以外はすべて自動化されており、しかも、後工程の加工ラインも自動化されているため、まさに検査工程だけがネックになっていた。
「キャリアは3つの部品をロウ剤で焼結し接合した部品です。焼結の際、金型を用いた成形工程で亀裂やひび割れといったクラックが入ることがあります。そのため、焼結炉から出てきたATキャリアはすべて目視検査していました。磁粉が入った液体にATキャリアを漬けて磁化させ、ブラックライトを当てて磁粉の溜まり具合で亀裂やひび割れを判別します。この検査には熟練技術が必要であり、検査員が熟練者を呼び出し確認を行うこともありました。一日あたり約1,000台生産するなか、ひとつのATキャリアがラインを通過する約45秒間で検査を行わなければならないため、どうしても人に頼らざるを得ません。しかも、2交代制でしたから常に2人の検査スタッフが必要です。言い換えると、ここを自動化できれば、製造~検査~加工工程の全自動ラインが実現すると考えました。」(渡辺氏)
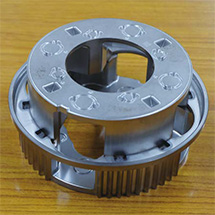
自動化のターゲットになった焼結部品のATキャリア
画角数の決定と不良品づくり
シーイーシーからWiseImagingのライセンスを購入し、2019年2月から本格的に検査工程の自動化に向けた取り組みが始まった。しかし、取り組む以前から、本社工場鍛造部以上に困難を極めることは予想していた。その理由は検査画角数の違いだ。本社工場鍛造部のフロントハブは2画角で対応可能だったのに対し、ATキャリアは形状が複雑なため、上下左右斜めから合計10画角が必要だった。
「焼結は粉を固めてつくっている特性上、どこにクラックが発生してもおかしくありません。不良品の発生頻度にかかわらず、常時シビアな検査する必要があります。」(渡辺氏)
「10画角という数は、実際に人が検査をしている作業場面を分析して割り出しました。そもそも人は角度を少しずつ変えながらさまざまな角度から見ることができますが、機械はそうはいきません。ですから、検査工程でひとつ当たりにかけられる約5秒間という限られた検査時間を考慮しつつ、その最大数として10画角を算出しました。
さらに困難を極めたのが不良品づくりだった。精度を高めるには、より多くの不良品をつくって学習させる必要がある。「前提として、不良品の検出率100%の精度が出なければインライン化することができません。その精度を高めるため、普段では設定しない条件で無理やりクラックがある不良品づくりの作業を行いました。目視で1mm程度の小さいクラックから数十mmの大きなクラックまで、それぞれ画角ごとに必要だったため、つくった不良品の数は1,000にも上ったと思います。しかも、生産ラインが稼働しているときは行えないので、休日を返上して不良品づくりに勤しみました。」(渡辺氏)
ノウハウを蓄積するやり方で進める
今回の取り組みのポイントは内製化だ。導入プロジェクトは、渡辺氏、宮内氏を中心とした素形材技術部門主導とし、シーイーシーには技術的なサポートを依頼しながらも、機械学習のノウハウ伝授をお願いした。その理由は、インライン化した後を考慮してのこと。「インライン化できたとしても、すぐに新たなチャレンジや課題が出てきます。その際、我々にノウハウがなければ、ちょっとしたことでもシーイーシーに依頼しなければなりません。それはスピードアップやコスト削減の妨げになりますから、やはり我々側にノウハウを蓄積していく必要があります。もちろん、シーイーシーにも協力を仰ぎ、我々にノウハウが貯まるやり方で進めていきました。」(渡辺氏)
取り組みの流れは2段階。まずは自動化を行う自動検査装置のベースづくりと、OK・NGをより明確化させるため、画像の前処理設定を行った。「自動検査装置の構成を検討するところから始めました。約45秒のサイクルに合わせる機器構成と、それに対応したプログラムをどうカスタマイズするのかがポイントでした。そこはGPUの処理能力を考慮しつつ、可能な限り並列で10画角を処理する方法をシーイーシーと一緒に模索しました。また、クラックを見極めるのに適した画像のトリミングを決め、各画角100~200枚程度の画像をWiseImagingに学習させました。最初の3画角をシーイーシーに行ってもらい、それを参考にしながら私の方で残りの7画角を学習させました。」(宮内氏)
インライン化後約5カ月は検証期間
その後、検査精度を向上させるフェーズに移行。ここでは、AIの学習に必要なパラメーターのベースを決めるため、10画角のうち半分の5画角をシーイーシーに依頼した。「我々が行った残り5画角についても、シーイーシーにアドバイスを受けながら、これで問題ないか確認しながら進めていきました。また、我々だけでなく、クラック検査の担当者を招き、クラックを判別する際のコツなど、製造側からの意見ももらいました。最終的に学習させた画像の枚数は、10画角合わせ、OK画像、NG画像ともに1万4,000枚前後。合計約3万枚もの画像を学習させました。」(渡辺氏)
こうした努力が実り、無事2020年8月にインラインに移行した。インラインといっても、すぐに本格稼働したわけではない。まずは検査スタッフがいるなかにWiseImaging搭載の自動検査装置を投入。WiseImagingによるOK・NGの判定にかかわらず、これまでと同様に検査スタッフが判定する期間を設け、本当にインラインで検査の自動化が可能かどうかの検証を行った。検証は約5カ月行い、その間は追加の学習もさせた。そしてついに2020年12月、WiseImagingを搭載した自動検査装置の本格稼働が始まった。
製品の導入効果
省人化と見逃し率ゼロ%を実現
ATのキャリアにおける検査工程の自動化に成功した素形材技術部。その効果は以下の通りだ。
<省人化を実現>
WiseImagingの自動検査装置のみで検査が可能になったため、目視検査を廃止できた。これにより、熟練技術に頼ることなく、安定的にクオリティの高い自動車をユーザーに提供するという目標に向かって、また一歩突き進んだ。
<見逃し率0%を実現>
見逃し率0%、過検出率は5%を達成。すべてのクラックを検出できている。「インライン化後、抜き取り検査を実施しました。結果、WiseImagingがすべての不良品をNGと判定しており、WiseImagingへの信頼度も大きく高まりました。」(渡辺氏)
<ラインタクトの自由度がアップ>
新型コロナウイルス感染症の影響は生産ラインにも影響が出ている。従来は月産2万台だった生産ラインを1万5,000台に落とすこともあったという。その場合、ラインタクトが変わるため、約45秒の検査工程は約70秒に変更される。
「人が作業を行う場合の問題は、余った約25秒の使い道であり、何らかの業務を組み込む必要があります。こうした編成効率を考えるのはかなり負担だったのですが、自動化を果たした現在は人が不要ですから、生産台数が減ったらラインをゆっくり流すだけです。人のことを考えることなく、自由にラインタクトを制御できるようになったのは大きな成果と言えます。」(渡辺氏)
<フレキシブルなシーイーシーの対応>
インライン化した後、多少のトラブルはあったが、国内メーカーであるシーイーシーの素早い対応により、大きな問題には発展しなかった。「海外製品の場合、イレギュラーなトラブルは契約外となり、対応に遅れが生じることが多々あります。その点、シーイーシーはフレキシブルに対応してくれます。二人三脚で進めていける安心感は何にも代えがたいと感じています。」
今後の展開と期待
不良品画像の自動生成技術に期待
素形材技術部にとって検査工程の自動化第一号となった今回のATキャリアの件は、「検査は自動化できる」「省人化ができる」という点で他のラインもモチベーションがアップしているという。今回の成功例をベンチマークに、さらに展開していこうという流れが見え始めた。
「焼結部品だけでもたくさんのラインがありますから、今後は自動化の流れが一気に加速していくと思います。我々もこれで終わりではなく、新たな自動化に向けて進んでいくつもりです。まず、今回のATキャリアとまったく同じものが別の工場で生産されていますから、その工場の2ラインを自動化したいと考えています。ただ、今回のようにNGとなる不良品をたくさんつくってその都度学習させる方法は、横展開させるには少し手間がかかり過ぎます。現在、シーイーシーと相談しているところですが、AIによる不良品画像の自動生成にも取り組んでいるとのことでしたので、その機能を含めて今後も積極的にご協力いただきたいと思っています。」(渡辺氏)
また、宮内氏は「検査以外のところでも人が介在する業務がいくつかあります。鍛造を例にすると、金型でプレスしているとき、一瞬見える金型状態の良し悪しを確認する作業です。こういった業務のように、人の目や技能に頼っている状態監視の部分も自動化できれば、より多くの省人化が図れるのではないかと考えています。」と語ってくれた。
※製品名・企業名・役職名など、記載の情報は取材時のもので、閲覧時には変更されている可能性があります。

世界最大級の自動車メーカー。2021年の米国市場の新車販売台数で初の首位を獲得し、世界の新車販売台数では2年連続トップを確実なものにしている。現在は「自動車をつくる会社」から「モビリティカンパニー」への移行を目指し、世界中の人々の「移動」に関わるあらゆるサービスを提供する会社、そして、移動の自由と楽しさを提供する会社に変革中。ホーム&アウェイ視点で、トヨタグループ全体の事業の再構築や従来の枠組みに捉われないモビリティサービス中心の協業を加速させている。
- 設立
- 1937年8月
- 本社
- 〒471-8571 愛知県豊田市トヨタ町1番地
- 資本金
- 6,354億円
- 従業員数
- 71,373人(連結 366,283人/ 2021年3月末現在)
- 主な事業内容
- 自動車の生産・販売
- URL
- https://www.toyota.co.jp